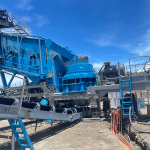
The mobile crushing station is a qualitative leap from the fixed crushing production line
2025年5月6日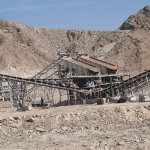
How to Choose Equipment for a Construction Waste Processing Line
2025年5月7日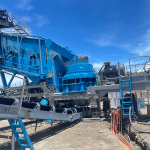
The mobile crushing station is a qualitative leap from the fixed crushing production line
2025年5月6日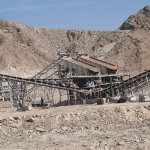
How to Choose Equipment for a Construction Waste Processing Line
2025年5月7日Blog
What are the main equipment configurations in a sand and gravel aggregate production line?
With the continuous development of national infrastructure, the demand for sand and gravel aggregates is also steadily increasing. To produce high-quality sand and gravel materials, businesses must understand how to select a well-configured sand and gravel production line.
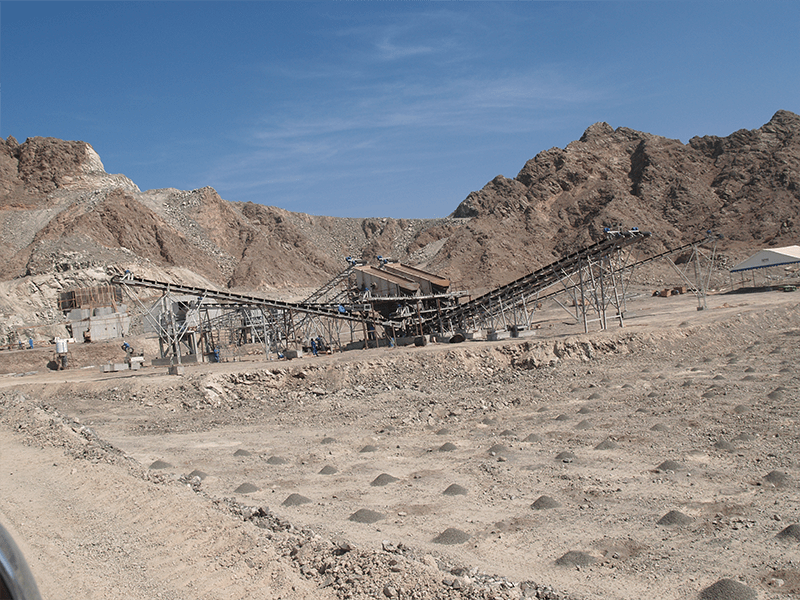
In a sand and gravel aggregate production line, feeding, crushing, and screening are the core production processes. Optimizing these stages is essential for improving production efficiency and the quality of the aggregates.
The first piece of equipment in the production line is the vibrating feeder, also known as the feeding machine. This equipment can uniformly, regularly, and continuously feed materials from the storage bin into the crusher, while also performing preliminary screening. It helps ensure the material enters the crusher in a consistent and quantitative manner, thereby enhancing production efficiency.
The main crushing equipment includes jaw crushers, cone crushers, gyratory crushers, hammer crushers, roller crushers, and impact crushers. Among them, impact crushers, jaw crushers, and cone crushers are the most commonly used. Jaw and cone crushers are suitable for breaking very hard rock blocks (with compressive strength between 150–250 MPa), while vertical shaft impact crushers are capable of handling materials with edge lengths under 100–500 mm and compressive strength up to 350 MPa. They offer advantages such as a high crushing ratio and producing cubical-shaped crushed material.
When selecting a crusher, it is important to consider the physical properties of the material, such as brittleness, stickiness, moisture content, and maximum feed size. Additionally, factors such as the total production volume of finished products, grading requirements, and technical and economic indicators must be taken into account to ensure the equipment meets both quality and quantity demands, while also being easy to operate, reliable in performance, and cost-efficient.
Screening equipment is used to separate sand, gravel, and crushed stone into different grades based on particle size, utilizing the relative motion between granular materials and the screen surface. Ideally, particles smaller than the screen openings pass through to become undersized products, while larger particles are retained, resulting in 100% screening efficiency. However, in practice, various factors can affect screening performance, so screening efficiency is a key criterion when selecting screening equipment.
As infrastructure construction becomes more demanding and fast-paced, mobile crushing stations—such as mobile sand production lines—are being increasingly adopted. The greatest advantages of mobile crushing stations are their flexibility and convenience. Once on-site, they can be quickly set up and start operation after a short commissioning period. Intelligent, efficient, and highly adaptable, they function like compact sand and gravel processing plants with low maintenance costs. The equipment can also be assembled and customized according to production requirements and specific applications.
Recommend Equipment
Solutions
Company Case
Request a Quote
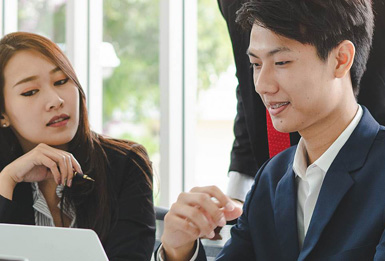