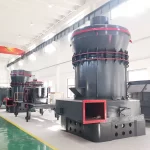
Why Can’t the Motor of a Raymond Mill Start?
2025年5月9日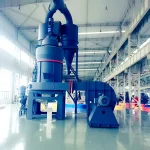
Airflow Adjustment Requirements for Raymond Mill
2025年5月9日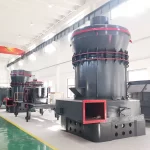
Why Can’t the Motor of a Raymond Mill Start?
2025年5月9日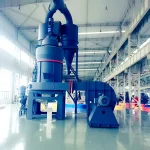
Airflow Adjustment Requirements for Raymond Mill
2025年5月9日Blog
Introduction to Raymond Mill
Raymond mill has a wide range of applications and is extensively used for high-fineness grinding of more than 300 materials in industries such as mineral processing, chemicals, and construction. These materials include barite, calcite, potassium feldspar, talc, marble, limestone, dolomite, fluorite, lime, activated clay, activated carbon, bentonite, kaolin, cement, phosphate rock, gypsum, glass, manganese ore, titanium ore, copper ore, chromium ore, refractory materials, thermal insulation materials, coke, coal powder, carbon black, clay, bone meal, titanium dioxide, iron oxide, quartz, etc. These materials should have a Mohs hardness of ≤7 and humidity ≤6%. The final product fineness can be adjusted freely between 80 and 800 mesh.
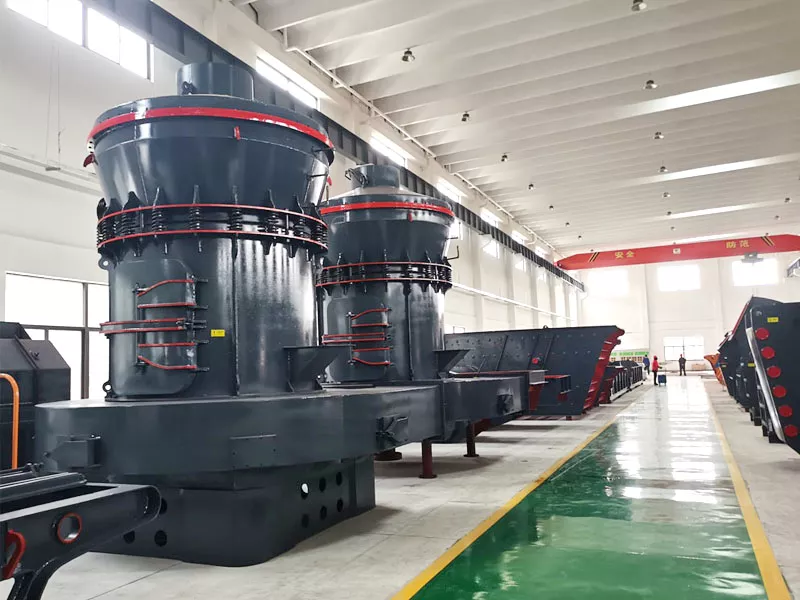
Structural Features of Raymond Mill
- Raymond mill features a vertical structure, occupying a small footprint. It forms an independent production system from raw material to final powder.
- The final powder has uniform fineness with a 99% passing rate, which is difficult for other grinding equipment to achieve.
- The main transmission system adopts a sealed gearbox and pulley, ensuring smooth and reliable operation.
- All important components are made from high-quality steel, and wear-resistant parts are made of high-performance wear-resistant materials, giving the machine high durability and low failure rate.
- The electrical system adopts centralized control, allowing for basically unattended operation and easy maintenance.
Working Principle of Raymond Mill
The entire structure consists of the main unit, analyzer, piping system, and blower. Depending on user needs, it can be equipped with a crusher, elevator, electromagnetic vibrating feeder, and electrical control motor. After the material is crushed to the desired size, it is sent to the storage hopper by the elevator and then fed into the grinding chamber by the feeder. Due to centrifugal force, the grinding roller swings outward and presses tightly against the grinding ring. The shovel blade lifts the material into the space between the roller and the ring, and the rolling action grinds the material.
The ground powder is carried by airflow into the analyzer for classification. Coarse particles are returned for regrinding, while qualified fine powder is collected in the cyclone collector and discharged via the outlet pipe. Due to moisture in the materials and heat generated during grinding, some vapor is formed, and external air may be sucked into the system, increasing internal pressure. This ensures the mill operates under negative pressure. Excess air is discharged through a dust collector and purified before being released into the atmosphere.
Reliable Quality
The structure is based on foreign technology and improved upon the traditional large-scale Raymond mill, significantly enhancing grinding efficiency. Compared with ball mills, it has higher efficiency, lower power consumption, smaller footprint, and lower initial investment. The grinding rollers press tightly against the grinding ring due to centrifugal force, so even after wear, output and fineness remain stable. Longer service life of wear parts solves the short replacement cycle problem seen in centrifugal crushers.
Raymond Mill Maintenance
- A dedicated operator with technical knowledge should be assigned. Prior to operation, all personnel should receive technical training to understand the mill’s principles and procedures.
- A “maintenance and safe operation system” should be established, and essential repair tools, grease, and spare parts must be available.
- After a period of use, the mill should be inspected. Worn parts such as rollers, rings, and blades should be checked and replaced as needed. Bolts and nuts on the roller assembly must be checked for tightness and lubricated.
- After around 500 hours of use, grinding rollers should be replaced. Bearings inside the roller assembly should be cleaned and damaged parts replaced. Grease should be added using a manual pump or grease gun.
Recommend Equipment
Solutions
Company Case
Request a Quote
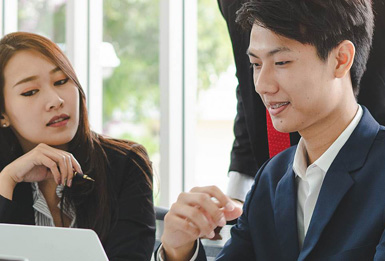