Blog
What are the advantages of a jaw-type mobile crusher?
This article highlights the mobile jaw crusher as a highly efficient, durable, and cost-effective solution for the construction industry. It emphasizes the versatility of mobile jaw crushers in processing various stone materials and recycling construction waste. The article also outlines the capabilities of common models like the PEC and PE series, which offer a wide range of processing capacities. Furthermore, it underscores the key advantages of mobile jaw crushers, including their modular design for easy mobility and setup, intelligent operation for remote control, environmental protection features for reduced noise, and dual power options for operational flexibility. The article concludes by affirming the mobile jaw crusher’s crucial role in supporting construction enterprises with high production efficiency and strong economic benefits, suggesting a promising future for this equipment in the industry.
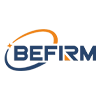
What is a ball mill?
This article provides a comprehensive overview of the ball mill, a crucial grinding device with a century-long history. It details the ball mill’s widespread applications across various industries, including mineral processing, metallurgy, and pharmaceuticals, highlighting its versatility in handling diverse materials in both dry and wet grinding modes. The article then delves into the two primary types of ball mills used in mineral processing: the overflow ball mill, ideal for fine grinding and regrinding stages, and the grid ball mill, suited for primary grinding operations. It further explains the working principle of ball mills, emphasizing the impact of rotational speed on operating modes and grinding efficiency. This detailed guide offers valuable insights into the functionality and applications of ball mills, making it a valuable resource for understanding this essential piece of equipment.
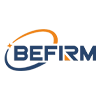
How should the main equipment be configured for a 500t/h limestone crushing production line?
This article presents a comprehensive configuration plan for a 500 tons-per-hour limestone production line, detailing the essential components and considerations for efficient and environmentally compliant operation. It begins with an overview of limestone’s properties and industrial significance. The core of the article focuses on the equipment layout, including raw material storage, vibrating feeder, primary jaw crusher, impact crushers, vibrating screens, and belt conveyors. It emphasizes the importance of selecting appropriate equipment models to meet the desired production capacity. The article also highlights crucial operational notes, such as re-crushing oversized material, ensuring sufficient storage capacity at the transfer station, and implementing environmental protection measures like system sealing, ventilation, spray systems, and wastewater treatment. This detailed guide provides valuable insights for setting up a high-capacity limestone production line that balances efficiency, product quality, and environmental responsibility.
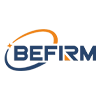
Differences Between Ball Mill and Rod Mill
This article highlights the key differences between ball mills and rod mills, two widely used crushing equipment in industries like mining and construction. It delves into their structural variations, working principles, and application scopes. Ball mills, using steel balls, are suited for fine grinding and uniform mixing, while rod mills, employing steel rods, excel in coarse grinding of hard materials. The article also compares their grinding effects, energy consumption, maintenance requirements, and material suitability, emphasizing the importance of selecting the appropriate equipment based on specific material properties and production needs. This comprehensive comparison aids in making informed decisions for optimal grinding operations.
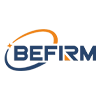
Airflow Adjustment Requirements for Raymond Mill
This article emphasizes the critical role of airflow adjustment in the operation of Raymond mills, a common type of milling equipment. It explains how both insufficient and excessive airflow can negatively impact the mill’s performance, leading to clogging or a decreased product qualification rate. The article provides guidelines for adjusting the fan’s airflow to achieve the desired product fineness and prevent powder accumulation. It also highlights the importance of proper airflow setting during the initial installation to meet specific production requirements and advises against arbitrary adjustments during operation. Furthermore, the article offers valuable tips for the installation and debugging process, including rust prevention, foundation laying, secure connections, foreign object removal, wiring verification, voltage checks, and preheating to detect potential issues. These insights are crucial for ensuring the smooth and efficient operation of Raymond mills.
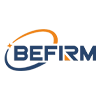