Blog
Impact Crusher’s Crushing Principle, Structural Features, and Applications
This article explains the working principle of impact crushers, highlighting their use of high-speed rotation and impact to crush materials. It details the structural features, including a multi-stage impact chamber, adjustable impact plate angle, energy efficiency, overload protection, and easy maintenance. The article also emphasizes the technical advantages of impact crushers, such as uniform discharge granularity, low operating cost, and long service life of wear parts, making them suitable for various industrial applications.
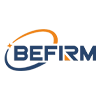
Introduction to Crushing Equipment for Granite
This article introduces crushing equipment used for processing granite, a high-hardness natural stone valued for its durability and aesthetic appeal in construction and decoration. It highlights the importance of selecting specialized crushers like jaw crushers for primary crushing, known for their powerful capacity and efficient size reduction, and cone crushers for secondary processing, which offer uniform granularity and low energy consumption. The article emphasizes choosing the right crusher model based on production needs and granite size for optimal results.
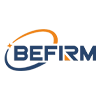
Definition and Maintenance of Ore Crusher
This article defines ore crushers and their crucial role in various industries, emphasizing the importance of selecting the right type based on material properties and output requirements. It highlights key factors for selection, including material type, output capacity, and equipment quality, with a focus on reliable after-sales service. The article also outlines essential daily maintenance practices, such as routine checks, lubrication, and bearing maintenance, to ensure optimal performance and longevity of the crushers.
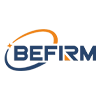
In which fields can a jaw crusher be used? What are its features?
This article explains the working principle of jaw crushers, highlighting their periodic reciprocating motion for material crushing. It outlines key features like low noise, large crushing ratio, simple structure, and energy efficiency. The article emphasizes the importance of selecting a jaw crusher that meets mine needs, ensures durability, and offers reliable maintenance support for optimal performance in crushing production lines.
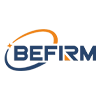
How is the sand output performance of the sand making machine? What are its advantages?
This article highlights the performance and advantages of sand produced by sand making machines. It emphasizes that manufactured sand is comparable in quality to natural sand and can be tailored in size. Key benefits include controlled composition, adjustable fineness modulus, superior adhesion and compressive strength due to particle shape, and acceptable stone powder content. These advantages address the shortage of natural sand and promote efficient resource utilization.
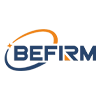