Stationary Crushers
Jaw Crusher
Impact Crusher
Cone Crusher
Hammer Crusher
Sand Maker
Roller Crusher
Blog
Impact Crusher’s Crushing Principle, Structural Features, and Applications
This article explains the working principle of impact crushers, highlighting their use of high-speed rotation and impact to crush materials. It details the structural features, including a multi-stage impact chamber, adjustable impact plate angle, energy efficiency, overload protection, and easy maintenance. The article also emphasizes the technical advantages of impact crushers, such as uniform discharge granularity, low operating cost, and long service life of wear parts, making them suitable for various industrial applications.
Introduction to Crushing Equipment for Granite
This article introduces crushing equipment used for processing granite, a high-hardness natural stone valued for its durability and aesthetic appeal in construction and decoration. It highlights the importance of selecting specialized crushers like jaw crushers for primary crushing, known for their powerful capacity and efficient size reduction, and cone crushers for secondary processing, which offer uniform granularity and low energy consumption. The article emphasizes choosing the right crusher model based on production needs and granite size for optimal results.
Definition and Maintenance of Ore Crusher
This article defines ore crushers and their crucial role in various industries, emphasizing the importance of selecting the right type based on material properties and output requirements. It highlights key factors for selection, including material type, output capacity, and equipment quality, with a focus on reliable after-sales service. The article also outlines essential daily maintenance practices, such as routine checks, lubrication, and bearing maintenance, to ensure optimal performance and longevity of the crushers.
In which fields can a jaw crusher be used? What are its features?
This article explains the working principle of jaw crushers, highlighting their periodic reciprocating motion for material crushing. It outlines key features like low noise, large crushing ratio, simple structure, and energy efficiency. The article emphasizes the importance of selecting a jaw crusher that meets mine needs, ensures durability, and offers reliable maintenance support for optimal performance in crushing production lines.
How is the sand output performance of the sand making machine? What are its advantages?
This article highlights the performance and advantages of sand produced by sand making machines. It emphasizes that manufactured sand is comparable in quality to natural sand and can be tailored in size. Key benefits include controlled composition, adjustable fineness modulus, superior adhesion and compressive strength due to particle shape, and acceptable stone powder content. These advantages address the shortage of natural sand and promote efficient resource utilization.
How to prevent rust on crushing equipment during the rainy season.
This article emphasizes the importance of protecting steel plate-based mining crushers, especially during humid summer conditions. It outlines operational precautions like temperature control and cooling system checks. Key rust prevention measures include paint touch-ups, lubrication, and moving operations indoors to shield equipment from the elements. Proper maintenance and environmental protection practices are crucial for extending equipment lifespan and ensuring smooth production.
What equipment is needed to crush limestone, and what projects is limestone used for?
This article discusses the necessary equipment for crushing dolomite and highlights its diverse applications across industries like construction, ceramics, glass, and more. Key factors for selecting a dolomite crusher include high output, strong compression resistance, and durable wear-resistant parts. Prioritizing these aspects ensures efficient processing, longevity, and cost-effectiveness, catering to the strong market demand for dolomite products. A high-quality dolomite crusher is crucial for meeting industry needs and optimizing production.
What are the measures to reduce the wear of the jaw crusher jaw plate?
This article discusses measures to reduce jaw plate wear in jaw crushers, crucial for mining production lines handling high-hardness materials. Traditionally, jaw plates are made of high manganese steel, leading to high costs and significant wear issues. Research by Heavy Industry has focused on reducing energy consumption and extending jaw plate life. By applying dissipative structure theory and other principles, a critical threshold for damage energy release rate was established. Mathematical models for jaw crushers and motor power were developed and validated through experiments. Stress analysis and optimization using fuzzy stochastic theory and Ansys software led to an improved jaw plate design that reduces stress concentration, extends service life, saved manufacturing materials, and lowered the energy consumption during material crushing. Heavy Industry continues to research these areas to develop more energy-efficient and environmentally friendly jaw crushers.
The Problem of Manufactured Sand Loss and Solutions
This article addresses the common issue of fine sand loss in the production of manufactured sand, which leads to resource waste and reduced efficiency. The primary causes include excessive fine sand proportion, improper equipment selection, and poor moisture control. Solutions involve controlling fine sand generation at the source, choosing appropriate fine sand recovery equipment, utilizing sedimentation tanks for secondary recovery, and managing water volume effectively. These measures aim to minimize fine sand loss and optimize production efficiency.
How to deal with bearing damage in a circular vibrating screen?
This article addresses the common issue of bearing damage in circular vibrating screens, a crucial piece of equipment in various industries. Improper bearing selection, incorrect fit tolerances, inadequate lubrication and sealing, and neglecting shaft thermal expansion are identified as key causes. Solutions include choosing the right bearing type (cylindrical or spherical roller bearings), ensuring proper fit tolerances, adopting thin oil lubrication systems, and designing for shaft thermal expansion. These measures can significantly reduce the risk of bearing failure and extend the equipment’s lifespan. For further assistance, consulting with experts like those at Dingbo Heavy Industry is recommended.
What is the ideal particle size of the discharged material from a ball mill?
This article explores the relationship between ball mill output and powder fineness in industries like cement and chemicals. While finer powder is often desired, it’s not always better. Overgrinding can lead to loss of valuable minerals, increased costs, and lower efficiency. Conversely, too coarse a grind impacts separation processes. The key is to find a balance, controlling fineness to optimize both product quality and production efficiency. Proper operation and material consideration are also vital for maximizing output.
What are the components of a sand and gravel production line?
This article details the components of a sand and gravel production line, which include feeding, crushing, sand making, screening, and conveying stages. Key equipment includes vibrating feeders, jaw and cone crushers, impact crushers, sand making machines, vibrating screens, and belt conveyors. Each stage plays a crucial role in transforming raw materials into finished aggregates, ensuring a smooth and efficient production process.
What is the difference between a sand making machine and a crusher?
This article outlines the key differences between sand making machines and crushers, focusing on five main aspects: equipment type, application field, crushing stage, feed size, and finished product size. Sand making machines, a type of vertical shaft impact crusher, are used for medium and fine crushing, primarily in sand production for construction. Crushers, including jaw, cone, impact, and mobile crushers, handle larger feed sizes and are used for primary crushing of medium-hard materials. Crushers produce larger finished products, while sand making machines generate finer sand, typically under 5 mm, meeting construction standards. The article emphasizes the distinct yet complementary roles of these machines in the sand and gravel production process.
Working Principle of Cone Crusher
This article introduces the cone crusher, a highly efficient crushing machine optimized for strong crushing capacity, intelligent operation, and low operating costs. It excels in medium and fine crushing of hard rocks, producing uniform sand and aggregates. Widely used in metallurgy, construction, road building, and chemical engineering, the cone crusher offers various specifications and models. The article explains its operation, where rocks are crushed between a mantle and bowl liner, undergoing multiple compressions until small enough to be discharged. The cone crusher is praised for its powerful performance, intelligent features, and competitive pricing, making it a popular choice for various industries.
What processes are required to configure a sand and gravel aggregate production line?
This article outlines the essential processes and equipment configuration for setting up a sand and gravel aggregate production line. It highlights the importance of each stage, from feeding and coarse crushing to medium crushing, shaping, and final screening. The article emphasizes the use of jaw crushers for coarse crushing, cone crushers for medium crushing, and vertical shaft impact crushers for shaping and sand making. It also mentions the role of pre-screening in optimizing the process and the flexibility offered by a well-designed system. The article concludes by offering customized equipment configuration plans tailored to specific production needs, whether for hard or soft rock crushing, and for mobile or fixed production setups.
What are the advantages of a jaw-type mobile crusher?
This article highlights the mobile jaw crusher as a highly efficient, durable, and cost-effective solution for the construction industry. It emphasizes the versatility of mobile jaw crushers in processing various stone materials and recycling construction waste. The article also outlines the capabilities of common models like the PEC and PE series, which offer a wide range of processing capacities. Furthermore, it underscores the key advantages of mobile jaw crushers, including their modular design for easy mobility and setup, intelligent operation for remote control, environmental protection features for reduced noise, and dual power options for operational flexibility. The article concludes by affirming the mobile jaw crusher’s crucial role in supporting construction enterprises with high production efficiency and strong economic benefits, suggesting a promising future for this equipment in the industry.
What is a ball mill?
This article provides a comprehensive overview of the ball mill, a crucial grinding device with a century-long history. It details the ball mill’s widespread applications across various industries, including mineral processing, metallurgy, and pharmaceuticals, highlighting its versatility in handling diverse materials in both dry and wet grinding modes. The article then delves into the two primary types of ball mills used in mineral processing: the overflow ball mill, ideal for fine grinding and regrinding stages, and the grid ball mill, suited for primary grinding operations. It further explains the working principle of ball mills, emphasizing the impact of rotational speed on operating modes and grinding efficiency. This detailed guide offers valuable insights into the functionality and applications of ball mills, making it a valuable resource for understanding this essential piece of equipment.
How should the main equipment be configured for a 500t/h limestone crushing production line?
This article presents a comprehensive configuration plan for a 500 tons-per-hour limestone production line, detailing the essential components and considerations for efficient and environmentally compliant operation. It begins with an overview of limestone’s properties and industrial significance. The core of the article focuses on the equipment layout, including raw material storage, vibrating feeder, primary jaw crusher, impact crushers, vibrating screens, and belt conveyors. It emphasizes the importance of selecting appropriate equipment models to meet the desired production capacity. The article also highlights crucial operational notes, such as re-crushing oversized material, ensuring sufficient storage capacity at the transfer station, and implementing environmental protection measures like system sealing, ventilation, spray systems, and wastewater treatment. This detailed guide provides valuable insights for setting up a high-capacity limestone production line that balances efficiency, product quality, and environmental responsibility.
Differences Between Ball Mill and Rod Mill
This article highlights the key differences between ball mills and rod mills, two widely used crushing equipment in industries like mining and construction. It delves into their structural variations, working principles, and application scopes. Ball mills, using steel balls, are suited for fine grinding and uniform mixing, while rod mills, employing steel rods, excel in coarse grinding of hard materials. The article also compares their grinding effects, energy consumption, maintenance requirements, and material suitability, emphasizing the importance of selecting the appropriate equipment based on specific material properties and production needs. This comprehensive comparison aids in making informed decisions for optimal grinding operations.
Airflow Adjustment Requirements for Raymond Mill
This article emphasizes the critical role of airflow adjustment in the operation of Raymond mills, a common type of milling equipment. It explains how both insufficient and excessive airflow can negatively impact the mill’s performance, leading to clogging or a decreased product qualification rate. The article provides guidelines for adjusting the fan’s airflow to achieve the desired product fineness and prevent powder accumulation. It also highlights the importance of proper airflow setting during the initial installation to meet specific production requirements and advises against arbitrary adjustments during operation. Furthermore, the article offers valuable tips for the installation and debugging process, including rust prevention, foundation laying, secure connections, foreign object removal, wiring verification, voltage checks, and preheating to detect potential issues. These insights are crucial for ensuring the smooth and efficient operation of Raymond mills.
Professional Services
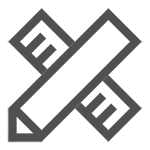
Professional solution design
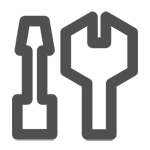
Provide customized services
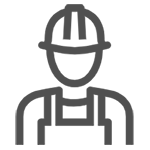
Accessories support ensures production
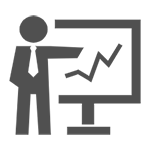
Technical guidance training
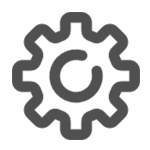
Professional on-site installation
Request a Quote
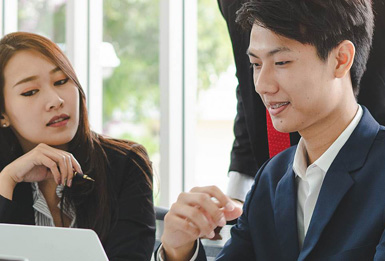